A biodegradable plastic
Biodegradable bags sound awesome, however they’re not without their issues. In 2014, for instance, a few individuals from the European Parliament made a decent attempt to achieve an entire restriction on oxydegradable plastics in the EU, with developing questions over their ecological advantages. Despite the fact that that proposition was blocked, it prompt more point by point investigations of oxydegradable plastics, clearly affirming that they can’t be adequately treated the soil or anaerobically processed and don’t for the most part separate in landfills. In the seas, the water is normally excessively cool, making it impossible to separate biodegradable plastics, so they either skim everlastingly at first glance (simply like customary plastics) or, on the off chance that they do separate, create little plastic pieces that are hurtful to marine life.
Reused plastic
One flawless answer for the issue of plastic transfer is to reuse old plastic materials (like utilized drain bottles) into new ones, (for example, things of attire). An item called ecoplastic is sold as a substitution for wood for use in open air plant furniture and fence posts. Produced using high-sub-atomic polyethylene, the makers brag that it’s durable, appealing, moderately shabby, and pleasant to take a gander at.
Open seat situate made of reused plastic with closeup of plastic woodgrain impact.
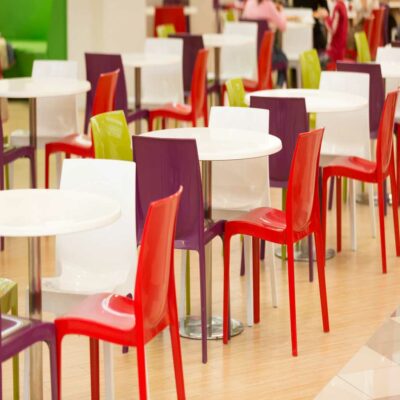
This “wooden” open seat looks much like some other until the point that you take a gander at the grain truly nearly. At that point you can see the wood is really reused plastic. The surface is persuading, however the giveaway is the finishes of the “boards,” which don’t look anything like the grain of wood.
Yet, there are two issues with reused plastics. To start with, plastic that is reused is for the most part not used to make similar things whenever around: old reused plastic jugs don’t go to make new plastic containers, yet bring down review things, for example, plastic seats and fence posts. Second, you can’t consequently accept reused plastics are better for the earth except if you know they’ve been made with a net sparing of vitality and water, a net diminishment in ozone harming substance outflows, or some other general advantage to the earth. Keeping waste out of a landfill and transforming it into new things is extraordinary, however imagine a scenario where it takes an immense measure of vitality to gather and reuse the plastic—more even than making shiny new plastic items.
Are bio plastic great or terrible?
Anything that enables mankind to tackle the plastics issue must be something worth being thankful for, isn’t that so? Lamentably, natural issues are never fully so straightforward. Activities that appear to help the planet in evident ways at times have significant disadvantages and can do harm in different ways. It’s critical to see things in the round to comprehend whether “earth well disposed” things are truly accomplishing more damage than great.
Bioplastics and biodegradable plastics have for quite some time been dubious. Makers get a kick out of the chance to depict them as an enchantment shot answer for the issue of plastics that won’t leave. Bioplastics, for instance, are touted as sparing 30– 80 percent of the ozone harming substance outflows you’d get from typical plastics and they can give nourishment longer timeframe of realistic usability in stores. However, here are a portion of the downsides:
At the point when some biodegradable plastics break down in landfills, they create methane gas. This is an intense ozone depleting substance that adds to the issue of a dangerous atmospheric devation.
Biodegradable plastics and bioplastics don’t generally promptly break down. Some need introduction to UV (bright) light or moderately high temperatures and, in a few conditions, can at present enjoy numerous years to reprieve down. And still, after all that, they may desert smaller scale pieces or lethal buildups.
Bioplastics are produced using plants, for example, corn and maize, so arrive that could be utilized to develop sustenance for the world is being utilized to “develop plastic.” By 2014, right around a fourth of US grain generation was required to have been swung over to biofuels and bioplastics creation; removing more agrarian land from creation could cause a critical ascent in nourishment costs that would hit poorest individuals hardest.
Developing harvests to make bioplastics accompanies the typical natural effects of escalated agribusiness, including nursery outflows from the oil expected to fuel cultivate hardware, and water contamination caused by spillover from arrive where composts are utilized as a part of mechanical amounts. Now and again, these backhanded effects from “developing” bioplastics are more prominent than if we essentially made plastics from oil in any case.
Some bioplastics, for example, PLA, are produced using hereditarily changed corn. A few earthy people think about GM (hereditarily changed) harvests to be characteristically hurtful to nature, however others oppose this idea.
Bioplastics and biodegradable plastics can’t be effectively reused. To a great many people, PLA looks fundamentally the same as PET (polyethylene terephthalate) be that as it may, if the two are stirred up in a reusing canister, the entire gathering winds up difficult to reuse. There are fears that expanding utilization of PLA may undermine existing endeavors to reuse plastics.
Numerous individuals think terms like “bioplastic,” “biodegradable,” and “compostable” mean the very same thing. Be that as it may, there’s a tremendous contrast between a “biodegradable” plastic (one that may enjoy decades or hundreds of years to reprieve down) and a genuinely “compostable” material (something that transforms on the whole into amiable waste following a matter of months in a composter), while “bioplastic,” as we’ve just observed, can likewise mean distinctive things. Befuddling language hampers open comprehension, which makes it harder for purchasers to get a handle on the issues and settle on positive decisions when they shop.
Instructions to eliminate plastic
Why is life never straightforward? In case you’re enthused about helping the planet, intricacies like this sound totally maddening. Yet, don’t give that put you a chance to off. The same number of ecological campaigners bring up, there are some extremely straightforward answers for the plastics issue that everybody can shoulder as a primary concern to have a genuine effect. Rather than just sending your plastics squander for reusing, recall the maxim “Diminish, repair, reuse, reuse”. Reusing, however significant, is just marginally superior to discarding something: regardless you need to utilize vitality and water to reuse things and you presumably make poisonous waste items also. It’s obviously better to decrease our requirement for plastics in any case than to need to discard them subsequently.
A Bic Evolution HB pencil produced using 57 percent reused plastic rather than wood.
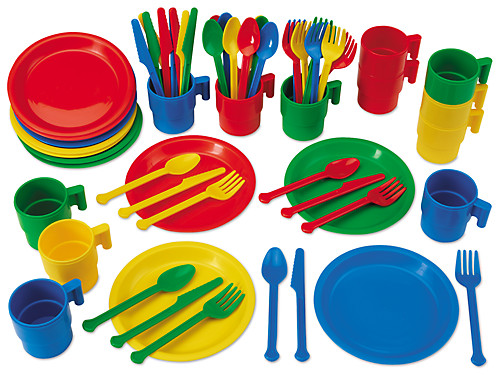
Recycling just works if it’s monetarily feasible. You can help make a business opportunity for reused items by currently picking them over choices. This Bic Evolution pencil, for instance, is produced using 57 percent reused plastic, which is a blend of pre-customer squander (a waste item from another industry) and post-shopper squander (reused family unit and office material).
You can have a beneficial outcome by currently eliminating the plastics you utilize. For instance:
Get a reusable cotton sack and take that with you ever time you go shopping.
Purchase your foods grown from the ground free, keeping away from the additional plastic on pre-bundled things.
Utilize dependable things, (for example, razors and refillable pens) as opposed to dispensable ones. It can work out far less expensive over the long haul.
On the off chance that you break something, would you be able to repair it just and bear on utilizing it? Do you truly need to purchase another one?
Would you be able to give undesirable plastic things another rent of life? Frozen yogurt tubs make awesome capacity compartments; candy machine glasses can be transformed into plant pots, and you can utilize old plastic grocery store packs for holding your litter.
When you do need to purchase new things, for what reason not purchase ones produced using reused materials? By making a business opportunity for reused items, you urge more makers to reuse.
Multi-day, we may have consummate plastics that separate in a trice. Until at that point, we should be more brilliant about how we utilize plastics and how we dispose of them when we’ve completed with them.