“What are suitable filler masterbatches for packaging ?” – If you are working in the packaging field, it must be a common question to help you find the suitable material for your end-products. In fact, the application of calcium carbonate filler in the packaging industry depends on many criteria, which makes it more challenging for plastic enterprises to find the right fits. In this article, let’s discover the top 4 most recommended types of filler masterbatches for packaging industry.
Filler masterbatch (also known as calcium carbonate filler) is an effective material solution for the plastic industry since it helps plastic enterprises significantly reduce production cost. As one of the biggest sectors in the plastic industry, packaging field is also one of the largest contributors to filler masterbatch consumption. The types of calcium carbonate fillers consumed vary among end-products because of the differences regarding their properties and technical requirements. This list below will summarize the top 4 most common types of filler masterbatches for packaging industry.
1. How does filler masterbatch benefit the packaging industry?
Filler masterbatch or calcium carbonate filler is one of the most important plastic fillers. It is the combination of calcium carbonate (CaCO3), which takes up over 70% of total weight, plastic resins and other specific additives. As CaCO3 is more reasonable than plastic resin, the application of CaCO3 into plastic combination reduces the amount of resins required, thus helping plastic enterprises save production cost. Besides, calcium carbonate also introduces various benefits to end-products such as shortening product’s cycle (thanks to CaCO3’s good thermal conductivity), and improving product’s mechanical properties (impact strength, tear resistance,…). For that reason, filler masterbatch is widely used in many applications in packaging fields such as shopping bags, wrapping films, roll bags, garbage bags,…
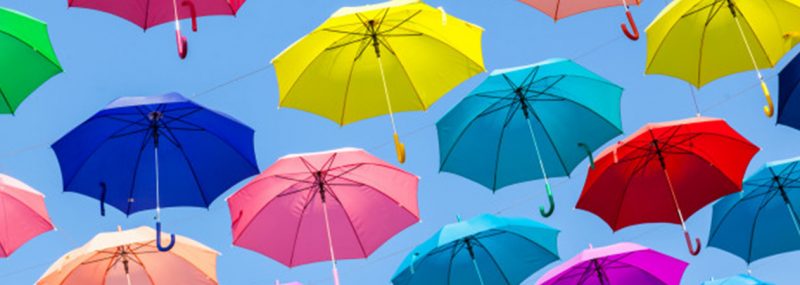
The thing is, why do we need to figure out appropriate types of calcium carbonate fillers? As each product has different technical requirements, only certain compatible types of filler masterbatch can meet those standards. As such, it is quite risky for plastic enterprises to randomly choose any types of filler masterbatch for packaging because it may result in end-product’s quality degradation.
2. Common types of filler masterbatch for packaging
PE filler masterbatch
PE calcium carbonate filler is made of PE resin, CaCO3 and other additives. It is a familiar type of filler masterbatch for packaging, especially in blown film thanks to its appropriate mechanical properties such as high ductility, impact strength and low friction. Most importantly, the application of PE calcium carbonate filler considerably reduces production cost, which lowers the price of end-products. Some common applications of PE filler masterbatch in blown film include shopping bags, T-shirt bags, garbage bags,… Furthermore, PE calcium carbonate filler is also used in manufacturing PP woven sack, multi-layer films,…
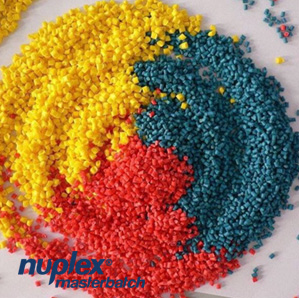
PP filler masterbatch
As the name suggests, PP filler masterbatch is composed of polypropylene resin, CaCO3 and other additives. It’s properties are similar to polyethylene, but it is slightly harder and more heat resistant. Hence, PP filler masterbatch is commonly used in PP woven sack and non woven products with a view to decreasing production cost and minimizing environmental effects of the manufacturing process.
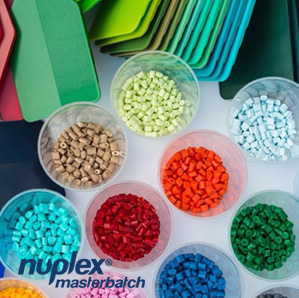
Transparent filler masterbatch
Another type of filler masterbatch for packaging is transparent filler, which is the combination of BaSO4 (Barium sulfate) or Na2SO4 (Sodium sulfate), plastic resins and other special additives. It can take both Polypropylene (PP) and Polyethylene (PE) as plastic carriers. Most plastic manufacturers use transparent filler to improve certain end-products’ properties such as stiffness, mechanical properties (bend strength, impact strength), tear resistance and most importantly, the whiteness. Thanks to the two components – barium sulfate/sodium sulfate, end-products are offered a beautiful brightness and transparency. Also, the use of transparent filler shortens the time required for each product cycle, thus facilitating production efficiency.
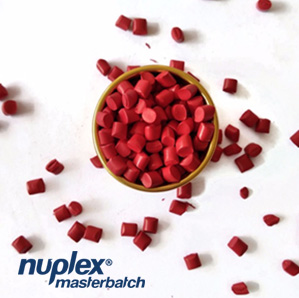
Thanks to these advantages, this material is widely used in many applications such as packaging films, containers, bottles, cans,…
Bio filler masterbatch
It would be such a pity if we miss bio filler masterbatch in this list. It is such an effective material solution to the packaging industry. Unlike other types of calcium carbonate fillers which include fossil resins, bio filler is mainly made of CaCO3 and bioplastic. This composition makes it completely environmentally – friendly, thus cutting down on the amount of waste released during plastic manufacturing production. Not only is it safe for the environment, bio filler masterbatch also offers end-products a firm structure and high tear resistance. Unlike other kinds of bioplastic, which easily go soggy in liquids, products made of bio filler masterbatch are tougher and more endurable even in the water. This advantage makes bio filler masterbatch specifically suitable for single-use products (cutleries, glasses, boxes, packaging films,…), which are consumed in bulk annually worldwide.
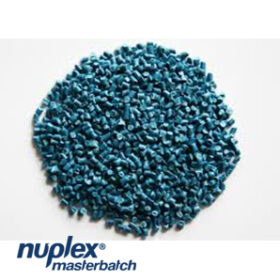
What else? Bio filler can also act as a processing aid when it comes to blown film process. This material can prevent the adhesion among film layers, thus streamlining this process as well as boosting production efficiency.
3. Things to note when choosing filler masterbatch for packaging
To figure out the most appropriate type of filler masterbatches for packaging, plastic enterprises need to consider the following questions:
- What is your end-product? Each type of product has different technical requirements that only a certain number of calcium carbonate fillers can meet. Hence, the filler masterbatch added must be compatible with the end-products.
- Which type of resin is used? As we all know, the processing temperature varies among different carriers, so it would be a disaster if your embedded material has a lower melting point than your resins.
- What is the thickness of your packaging film? It’s extremely important to let your supplier know whether your film is thick or not. If it has to be thick, then the usage rate of filler masterbatch should be greater than that of the thinner one, which is normally around 15-35%. The more amount of calcium carbonate filler is used, the thicker the film gets.
- How transparent is your film layer? If the film layer is required to be highly transparent, a larger amount of calcium carbonate filler should come into use and vice versa. As calcium carbonate filler more or less decreases the level of transparency of end-products, plastic enterprises should use it mindfully. In some cases, transparent filler will be an effective alternative to accelerate the level of brightness and transparency.