Filler masterbatch, especially calcium carbonate (calcium carbonate) masterbatch is considered as one of the most excellent objects in the plastics industry. Calcium carbonate filler masterbatch has a multitude of applications with the large number of products made from them. Here are the salient features and 4 most popular applications of this mastebatch.
What is a filler masterbatch made of calcium carbonate?
Calcium carbonate filler masterbatch is a mixture containing a large amount of fine calcium carbonate (CaCO3) powder mixed with a part of virgin plastic and some suitable plastic additives. The mixture is heated to high temperatures until it melts into a liquid form. After the ingredients in the mixture are mixed together, the mixture will be left to stand until it coagulates and passes through an extruder and finally chopped into small plastic particles. These plastic particles are the filler master batch. CaCO3 masterbatch is widely applied as a filler used in manufacturing and manufacturing plastic products. They function to replace a part of input materials, help manufacturers save costs and reinforce many features of the products made at the same time.
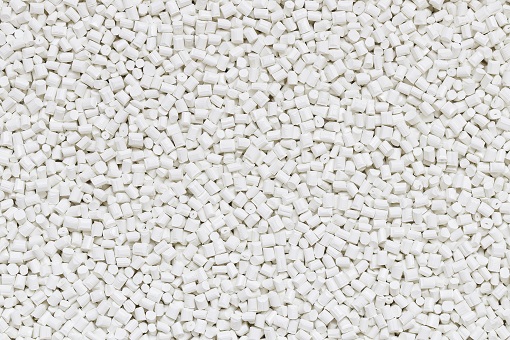
Calcium carbonate filler masterbatch is naturally white, but they cannot be used as coloring agents for resins (because whiteness is not enough). However, when combined with white masterbatch containing titanium dioxide (TiO2), they play an active role in increasing whiteness and enabling white pigments to be evenly dispersed in the plastic mixture. As a result, the finished product will achieve higher opacity than usual.
What are the superior features of calcium carbonate filler masterbatch?
Calcium carbonate powder makes up the majority of the masterbatch mixture, usually ranging from 60% to a maximum of 90%. They are most compatible with polyolefin (PP, PE) resins but can still be mixed with some other common resins such as PS, ABS, PVC, EPS, etc. This masterbatch filer was originally designed to be used as a filler providing economical and economical solutions for the entire plastic industry around the world. However, over time, as the demand for multi-purpose materials is increasing, these days they not only play a simple role as a filler but also become special plastic additives. Has the function of improving the physical and chemical properties of the base resin. In general, thanks to the appearance of masterbatch, the quality of plastic products has improved significantly.
Overview of the application of calcium carbonate filler masterbatch
In general, the variety of calcium carbonate masterbatch applications is immeasurable and it is difficult to list them all. Some of the most outstanding applications are HDPE blowing, raffia tape, tarpaulin production, High Density (HD) and Low Density (LD) fabrics from PP / PE based resins, LDPE / LLDPE / HDPE films , plastic interior / exterior, etc. However, these applications can be divided into several major groups based on the method of manufacture or the origin of the resin. In this article we divide them by production method criteria.
Use CaCO3 filler masterbatch in the production of non-woven fabric
The range of fields with products made from calcium carbonate nonwoven fabric is very large, ranging from medical care, personal care to hygiene, geotextile (fabrics capable of absorbing, separating). , filtration, protection, reinforcement and drainage are used in engineering industries such as irrigation, transportation, environment). Benefits of using calcium carbonate filler masterbatch additive in nonwoven production include:
- Improve product surface by
- Reduced luster effect makes the surface more matte, more opaque, leading to increased coverage of the fabric structure
- Natural white product not yellowing
- Improve material texture by
- Create a soft and soothing feel like cotton fabric, avoiding fingerprints when touched
- Create microscopic air vents to filter the air and absorb oil
- Enhanced thermal conductivity and mechanical strength
- Contributing to lower processing temperatures, from which manufacturers can achieve higher productivity as well as save energy and production costs at the same time.
- Easily combined with many different types of plastic base (thanks to good dispersion ability) and can be processed, shaped by many methods
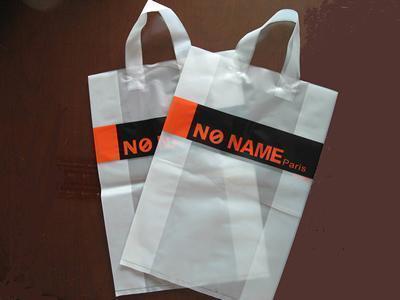
Treatment of calcium carbonate filler masterbatch by injection molding method
Calcium carbonate masterbatch mixed with PP base resin is the perfect solution for the production of household items such as furniture, containers, containers, bottles, jars, baskets, etc. through injection molding. The rate of CaCO3 in a PP resin mixture can be up to 50%. However, the exact formula for each production line should be carefully thought out and largely depends on specific requirements.
Besides calcium carbonate filler masterbatch with PP resin, other options for primary plastic sources are PS (polystyrene) and ABS. These are used in cases where surface scratches are acceptable. Products made from a mixture of PP and CaCO3 plastics through injection molding achieve thermal conductivity, better impact resistance, more flexible stiffness with less shrinkage.
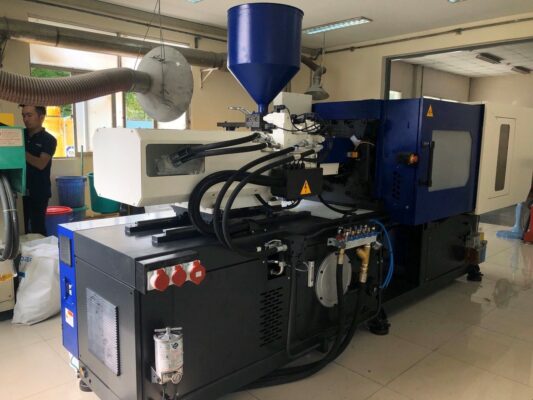
Apply CaCO3 filler mastebatch to extruded sheet and plastic film
With some special artificial materials such as LDPE, LLDPE or HDPE, calcium carbonate filler masterbatch can be added directly to the virgin plastic and these blends will work simultaneously as plastic fillers and plastic additives. Producing films and plastic sheets Basically, they provide higher non-stick, non-slip properties. The surface of the finished product will achieve an opacity suitable for printing. The tensile strength of the finished product is also improved, allowing their shape and structure to be fully protected even when they are stretched. Moreover, this material is safe to contact with food because it does not contain any harmful ingredients.
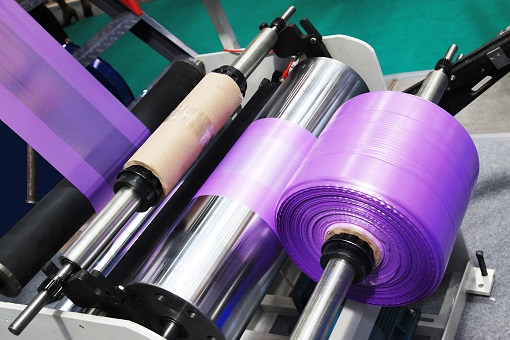
Calcium carbonate masterbatch is also found in spun yarns
CaCO3 filler masterbatch is said to be the perfect solution to help manufacturers partially or completely avoid the problem of fibers and fibers. Fiber yarn is one of the most common problems that manufacturers face in plastic and tape production processes. It causes the phenomenon of uncontrolled plastic structure separation when the PP / PE yarn is stretched. By adding only a small amount (3-4% of the total raw material content), the additive of calcium carbonate resin additive into the production of flat PP / PE fibers, not only is the problem of fibers and fibers solved, but also brings Some other benefits to this material include:
- Improving tensile strength and resistance to tearing, splitting of yarns, yarn twisted and woven fabrics after being stretched
- Provides anti-slip and non-sticking effect, facilitating the next winding step
- Improve weaving ability, welding ability and printing ability of materials
- Improving the rigidity of products makes them harder and more stable
- Less damage to machinery, especially the blade (by replacing the amount of titanium dioxide, nonstick and anti-slip agents used, which can cause abrasive effects on the blade). Generally, the service life of machinery is extended.
- Increase productivity
- Partially replacing the need to use a white masterbatch, thus helping manufacturers save costs
- Reduce input costs because calcium carbon masterbatch filler is much cheaper than other primary resins
- Easier handling
- Provides self-cleaning effect on other materials (like dyes) and machines (like extruders)